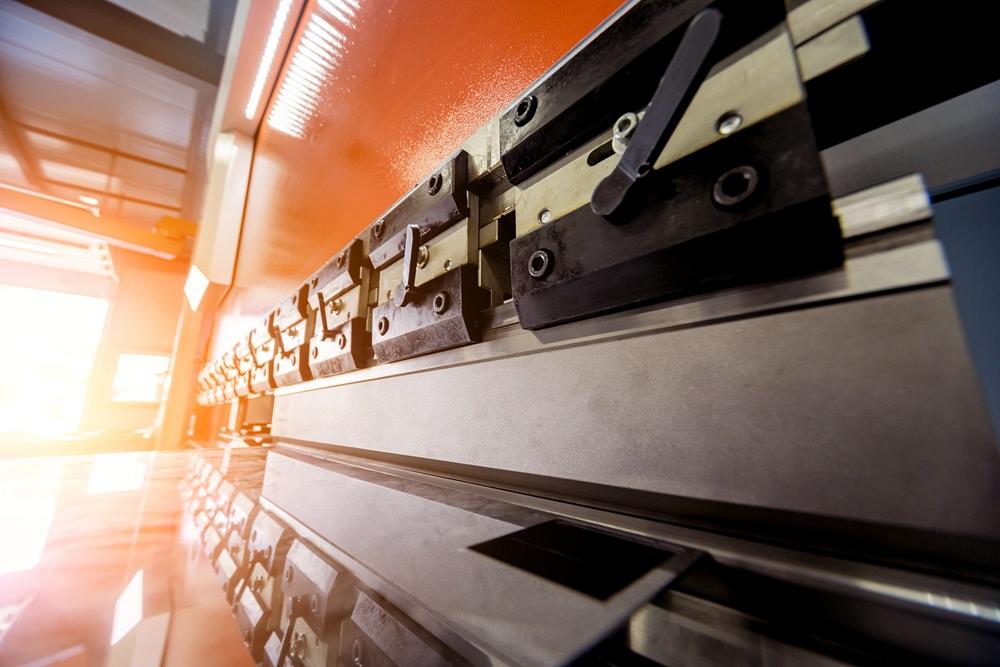
romaset/iStock/Getty Pictures Plus
Editor’s phrase: Be taught Half I, Half II, and Half III.
Over the previous couple of months, we’ve talked about how an air bend varieties as a result of the bend dimension will get longer on a press brake. In shorter bends, the radius varieties as a proportion of the die opening. In longer bends, the radius wraps throughout the punch nostril. Why does this happen? This sequence is digging deep, transferring into the weeds, and staring into the abyss to seek out the reply. We’re almost there.
Are You Nonetheless Air Forming?
If, as a result of the bend dimension grows, the radius not air-forms as a proportion of the die opening, are you proceed to air bending? The reply is certain … correctly, presumably. That’s decided by the tooling you make the most of to variety the material.
Assuming you are using precision-ground tooling, odds are you may nonetheless be air forming. For a lot of precision-ground tooling, the included die angle and punch angle are decrease than 90 ranges. If, say, your die angle is 88 or 86 ranges, your punch angle is on the very least 2 ranges decrease than that (see Decide 1). This creates angular clearance between the punch and die. Theoretically, you’ll bottom into an 88-degree die. If that happens, though, you’ll bottom-bend a 92-degree exterior bend angle (that is, an 88-degree inside bend angle, matching the die angle).
Precision-ground punches and dies will be discovered with 90-degree angles, and if that’s the case, you’ll be bottoming your longer bends. The an identical holds true for those who occur to’re using typical planer devices, for which the dies are almost universally 90 ranges. This makes the probability of bottoming very extreme, and it’s typically a typical observe for these using them.
In case your tooling angles are chosen for air forming, then even for those who occur to have been to bottom the punch into the die totally, you may nonetheless don’t have any contact between the die and punch faces. Which signifies that although you are penetrating deeper into the die space, you are nonetheless air forming.
Supplies Parts
Crystal measurement and supplies inclusions may also impact how the bend radius transitions from a traditional air bend to 1 by which the material wraps throughout the punch nostril. These crystals and inclusions are inside the grain of many different provides after rolling. Not all supplies has a grain, in spite of everything, nevertheless for individuals who do, the bend angle can change counting on the bend line’s relationship to the grain route.
The bend line may presumably be perpendicular, diagonal, or parallel to the grain route, and these properties can impact the radius transition in longer bends. That’s on account of bending all through (perpendicular to) the grain requires further energy to complete and has the next amount of springback.
Bending with the grain (that is, the bend line runs parallel to the grain route) requires a lot much less energy to complete and produces a smaller amount of springback. A with-the-grain bend usually requires a much bigger inside radius to keep up the material from cracking on the pores and skin of the bend.
Accounting for the Transition
We all know how the radius varieties transitions in prolonged bends, from a traditional air bend (with the radius forming as a proportion of the die opening) to 1 the place the radius wraps throughout the punch nostril. Can you calculate exactly when this transition takes place? You might—nevertheless do you actually wish to? No.
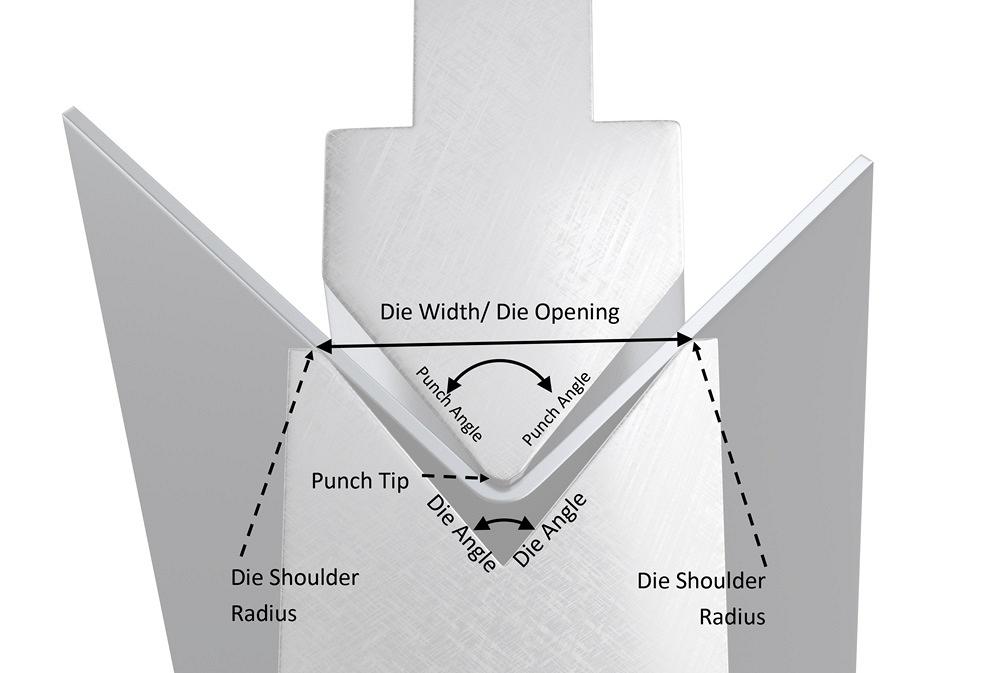
FIGURE 1. Air bend tooling setups have clearance between the punch angle and die angle.
Optimistic, you’ll write an algorithm that considers the bending second and the way in which the forces are affected by strain hardening. You would presumably calculate the facility will improve over the bend dimension and why it is important to reinforce the bending energy over a specific dimension because of the lack of energy to machine flexing. You would presumably embrace all these parts and additional—nevertheless as soon as extra, it’s merely non-compulsory.
The ability being added to compensate for an prolonged bend is bigger than the linear tonnage per foot price, nevertheless it’s solely enough to compensate for the loss due the flexing loss inside the press brake side frames—although you elevated the facility and penetration into the die space. In essence, you are balancing the forces out.
Although you are solely balancing for the dearth of vitality to the physique, these forces nonetheless set off the material to strain or work harden. That’s on account of the material being customary feels all of the rise in energy as the entire vitality passes by means of it, sooner than the machine flexing takes it away. Stress hardening reduces the material’s means to stream, however brute energy from the press brake overcomes that hardening. This causes the material to wrap throughout the punch nostril.
With all that being talked about, why don’t we have now to ponder all of this and calculate an precise reply? The reason is simple: The final word amount of change inside the bend radius, along with its impression on the bend allowance and bend deduction, shall be smaller than the variations you may face from the tolerances found spherical either side of the sheet metal. Nonetheless, merely because you don’t should calculate it doesn’t suggest you shouldn’t account for it.
Perceive that the radius transitions are there and that they’re typically merely adjusted for as a result of their minimal amount. Certain, the radius will get smaller as a result of it transitions from “floating” (forming as a proportion of the die opening) to wrapping throughout the punch nostril. Take a look at your mission and any extenuating circumstances and estimate how a smaller bend radius will impact the bend deduction and bend allowance.
Look at the Radius
You must use shop-grade pin gauges to confirm the radius. They aren’t low-cost, though, they often are more likely to get misplaced when used on the shop floor. Regular radius gauge models, metric or imperial, are sometimes too restricted for checking an air-formed bend.
Your solely possibility is usually to simply make a personalized radius gauge or gauge set. You might draw one in CAD and scale it up or proper all the way down to create a whole set, or draw one for a specific job, then ship it to your laser chopping or waterjet machine. For those who occur to decrease a job-specific gauge, place it inside the job traveler. That method, you presumably can quickly gauge the inside bend radius. One different profit: For those who occur to make a radius gauge your self and end up dropping it, you presumably can trade it merely.
As soon as extra, reaching a specific radius is essential for proper, repeatable bending—subsequently the importance of checking it. The patron might not care in regards to the bend radius, nevertheless you must, significantly for those who occur to’re making precision elements. When the radius modifications, so does all of the issues else: the bend allowance, the bend deduction, the flat clear measurement, and the last word half dimensions.
All Regarding the Radius
So, what was the aim of this sequence? For one, it was to increase the general details about sheet metal forming. Additional important, it communicates the importance of understanding and monitoring the inside bend radius. The bend radius modifications in an air variety; it is on no account mounted. Regardless, it stays an essential part of one thing manufactured from sheet metal requiring a bend—significantly if making tight-tolerance, precision elements is your goal.
Predict and calculate the last word radius, receive it inside the workpiece, and you may on a regular basis be succesful to make elements as close to good as humanly doable.
For those who occur to walk away finding out nothing further than merely how important the inside radius of the bend is—that it is important to calculate for it, receive that radius, and measure it to ensure its correctness—then you definately undoubtedly get your complete stage of this practice. Now, let’s stop staring into the abyss, get out of these weeds, and go assemble some good elements.