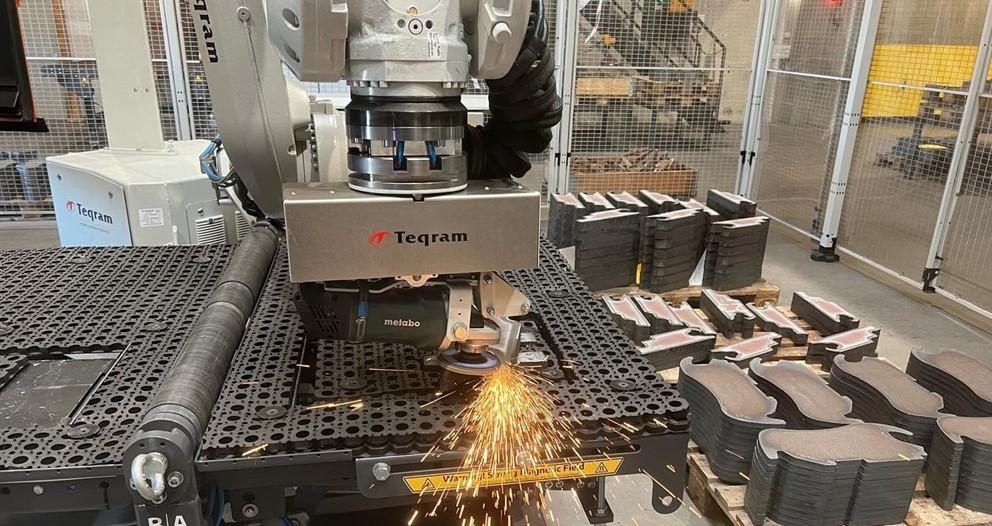
State of affairs
Martin GmbH, a subsidiary of Huppenkothen, manufactures about 20,000 excavator attachments yearly, along with quick-change packages, buckets, and hydraulic couplings. Meeting this amount requires optimum effectivity at every stage of producing.
The Ludesch, Austria-based agency cuts sheet metallic blanks from 8 to 70 mm thick using a plasma and flame-cutting system to produce parts for excavator buckets. Beforehand, a lot of employees have been liable for getting ready these parts by eradicating slag with chisels and grinding surfaces with angle grinders. This handbook method was not solely labor-intensive however moreover bodily demanding, with some parts weighing larger than 50 kg. Staff wanted to endure prolonged hours of coping with vibrating devices whereas turning heavy elements, contributing to extreme bodily stress.
“Discovering workers for such heavy, monotonous duties was already tough,” said Herwig Koch, Martin’s operations and know-how supervisor. “On prime of that, sick go away incessantly disrupted operations.”
Choice
The turning stage received right here when representatives from Martin discovered Teqram’s automated system at EuroBLECH 2022. “A robotic that operates with out programming? That immediately caught our consideration, given our quite a few product fluctuate,” Koch recalled.
Since July 2024, the company has used a Teqram EasyGrinder system that completely automates its deburring and shotblasting operations. This shift has improved manufacturing effectivity significantly and has enhanced working circumstances for employees.
Operators place flame-cut parts on Euro pallets and choose the desired processing top quality; the robotic handles all of the issues from slag eradicating to edge grinding or making a 2-mm radius. Equipped with autochanging devices, the system turns and grips the parts to help assure seamless, completely automated processing.
After deburring and grinding are achieved, a Rösler rotary desk system takes over for shotblasting. The Teqram robotic mechanically arranges the parts for blasting effectivity and restacks them on pallets after processing.
The system performs all processing and delivers ready-to-install elements with none programming or handbook intervention, making it the suitable match for Martin’s small to medium batch sizes and frequent workpiece changes.
Using 3D imaginative and prescient sensors and the EasyEye system, the robotic identifies the contours of the workpieces without having CAD drawings. It calculates the load and selects the appropriate gripper based on the material and geometry. The EasyFlipper then turns the half for processing on both facet.
By automating manufacturing, Martin has optimized its processes, serving to to ensure high-quality, reliable merchandise whereas bettering working circumstances. Automation moreover has made the company a additional participating employer by assuaging the bodily burden on its workers.