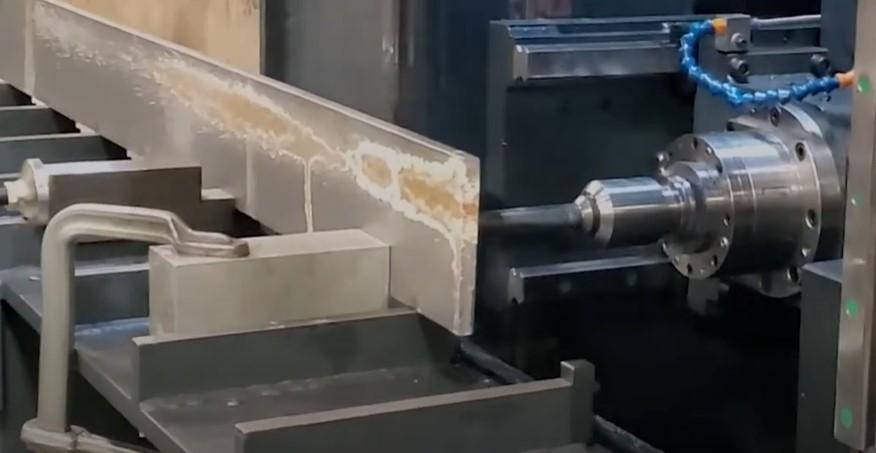
Gulf Coast Welding, Foley, Ala., has had a FlexBeam FB-40-42 since 2021, and it’s helped the shop improve its manufacturing functionality in anticipation of future progress. Flex Machine Devices
If doing the similar issue ends in the similar outcomes, that explains why many metal fabricators proceed down that acquainted path. It’s comfortable and, usually, helps to keep up the enterprise afloat.
Nonetheless when it’s time to take the following step, some hazard is anxious. Rising product sales and rising the enterprise require shaking up the established order. Solely a particular technique may end up in a particular finish consequence.
Ryan Maley and his enterprise companions purchased Gulf Coast Welding, Foley, Ala., from Maley’s dad in 2021. The metal fabricating enterprise, primarily based inside the mid-Nineties, had carved out a worthwhile space of curiosity engaged on heavy-duty jobs, comparable to structural metallic for residential and enterprise constructing and instruments for shut by manufacturing and processing firms. Gulf Coast Welding moreover provided self-discipline corporations, comparable to structural metallic erection, staircase and platform arrange, and welding restore. The company had a robust foundation of glad purchasers, and its location was close to rising areas in Georgia, Florida, and its Alabama residence. Nonetheless the model new homeowners moreover seen the prospect for further and launched right into a plan to deal with new markets.
A kind of latest areas was supporting duties for governmental our our bodies, identical to the Alabama Division of Transportation. Loads of these duties often take years to materialize, nevertheless as quickly as a retailer develops an understanding of what is required and useful properties a recognition for top of the range work and effectively timed responsiveness, it can probably cultivate work from that sector on a continuing basis. Maley said it has been a nice and common choice to develop along with diversify Gulf Coast Welding’s purchaser base.
With this consider rising the shop’s work, Maley acknowledged that some type of automation on the shop floor could help to boost manufacturing functionality whereas allowing the company’s knowledgeable welders to focus on further superior work. Gulf Coast Welding employs 20 people.
“Greater shops seem to go after jobs in a certain tonnage fluctuate. Then the really small shops can’t pretty get into the type of work that we do,” said Maley, describing the place Gulf Coast Welding matches into the world’s metal fabricating group.
The company had no wish to chase after the work that loads larger structural metallic firms lived off of, nonetheless it did just like the idea of utilizing the type of know-how that just a few of those large structural metallic fab shops wished to be aggressive. One thing that may expedite the processing of beams would help. The large supplies coping with strategies that moved beams from one station to the following and any robots weren’t the principle goal. This was to be the 1st step in direction of further setting pleasant days.
Flexibility in Beam Processing
At FABTECH in 2018, Maley seen a beam processing machine that caught with him. He immediately realized the affect that such a machine may need on a retailer, nevertheless this was sooner than he began overseeing Gulf Coast Welding’s operations.
“It merely stayed behind my ideas all of those years,” he said.
What Maley seen was an early-generation model of a CNC beam processing machine from Flex Machine Devices that provided precision drilling and milling capabilities. For any individual whose day job involved laying out and manually drilling a great deal of holes in structural beams, it’s no marvel he nonetheless remembered that machine so just a few years later.
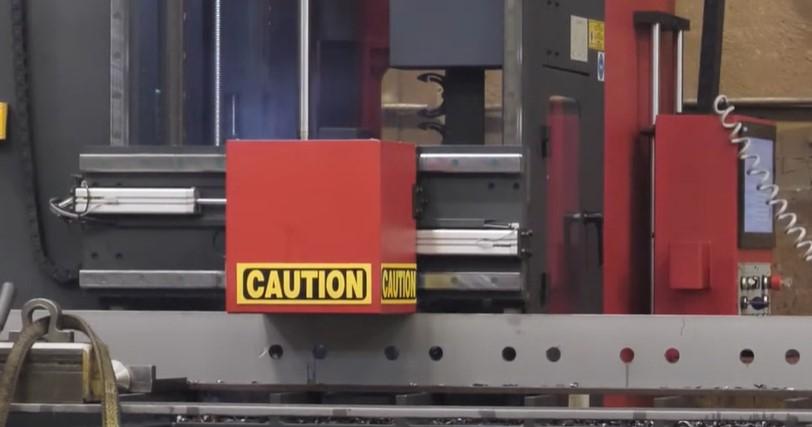
Gulf Coast Welding has found automated drilling of holes to be a dramatic enchancment in fabricating effectivity when as compared with handbook hole construction and drilling with a magnetic drill. Flex Machine Devices
Spurred on by the model new course of the enterprise, Maley and his companions purchased a FlexBeam FB-40-42 in late 2021. The machine, with a 40-ft.-long mattress, is ready to drilling, milling, tapping, and scribing. It has an computerized instrument changer that will accommodate six devices.
The horizontal drilling coronary heart is unique inside the metalworking commerce in {{that a}} horizontal foot comes down to hold the workpiece in place. That’s in distinction to typical vertical machining amenities whereby vises are wished to keep up the workpieces in place all through metal elimination.
“We talked to them regarding the machine, after which we went to see plenty of of them. As we checked out it, we merely felt want it was one factor that was compulsory for us, with the tales of labor shortages and all of the issues else. It merely appeared like a clear reply for what we had been making an attempt to do,” Maley said.
Upon arrange, the machine started to make an instantaneous affect. It merely delivered in a signifies that handbook drilling couldn’t match, in accordance with Maley.
For instance his stage, Maley described a job that Gulf Coast Welding obtained to fabricate some “lids” for an interstate enterprise. The fabrications, plenty of beams positioned side by side after which bolted collectively, cowl trenches inside the avenue and allow vehicles to drive over the trenches with out inflicting harm to vehicle suspensions. This job wasn’t basically very large by the use of gadgets, nonetheless it required quick turnaround on account of taxpayers don’t benefit from being delayed in guests as a result of constructing.
Each of the 26 lid assemblies had about 120 holes, which meant there have been 3,120 holes to drill. (Maley indicated that the enterprise moreover included holemaking on some plate that was part of the assemblies, nevertheless he didn’t embrace that as part of this occasion.)
Maley estimated that if the job wanted to be carried out manually, the tactic to create each hole—laying it out, organising the magnetic drill, and drilling the outlet—would have taken about 5 minutes. Working at that brisk tempo, the fabricator would have wished 260 hours to drill all 3,120 holes. That’s about six and a half weeks of labor for one particular person, with out further time, in any case.
Using the FlexBeam, Gulf Coast Welding was ready to drill a spot every 30 seconds, ending your complete job in 26 hours. It moreover accomplished the job with none doubts that the holes had been the place they wished to be. The automated drilling presents a consistency and velocity {{that a}} handbook fabricator can’t match.
“We wouldn’t technique a job like that if we didn’t have that machine,” Maley said.
In a single different event, the company was approached to do some ground milling on inlet drainage grates for a check out observe belonging to a vehicle producer. Similar to the interstate trench covers, this was one different rush job.
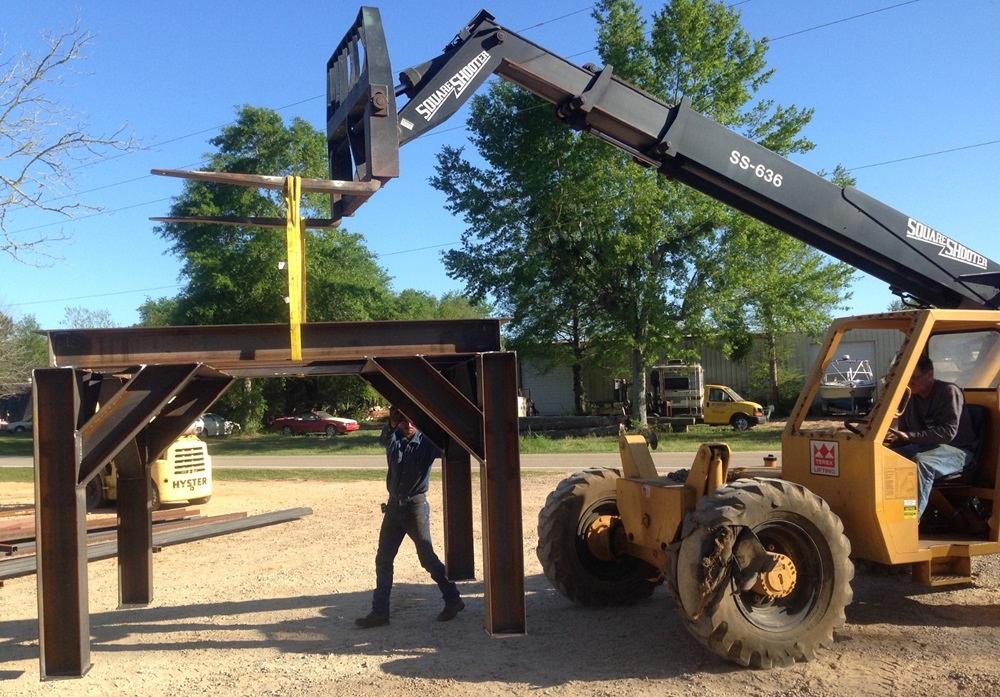
Industrial purchasers characterize an outstanding portion of Gulf Coast Welding’s beam fabricating work. Gulf Coast Welding
The grates, each weighing about 100 lbs., required bolt holes to keep up them in place as automobiles raced over them. Maley said his workforce was ready to configure some fixtures that held these grates vertical on the FlexBeam.
Plenty of of them had been prepare on the machine at one time. As a result of the gantry moved from one grate to the following milling the holes, the machine operator was ready to swap out the finished grates with new blanks. When it reached the tip, the gantry returned to the alternative end and commenced milling as soon as extra.
“It’s been a fairly versatile machine for us,” Maley said.
In a closing occasion, Maley recalled but yet one more transportation-related job whereby structural beams had been bolted vertically on the side of the bridge with barrier rails linked to them. These beams wished holes utterly aligned on all sides of the flange.
Even with the FlexBeam, Maley said he initially thought a beam have to be flipped all through processing so that the drill would possibly attain all sides of the 6-in. beam. Nonetheless, he discovered that by using an prolonged bit, the machine would possibly drill every holes concurrently with out having to flip the beam.
“We on no account wanted to concern about alignment on account of it was held within the similar place and drilled straight by the use of,” he said. “In the event you don’t have to worry about any misalignment of holes, that’s an outstanding issue.”
A New Custom of Automation
Metal fabricators are used to figuring out choices to points. As a consequence of that, they’re used to relying on their very personal wits and experiences. They don’t mechanically get your hands on an proprietor’s handbook after they get a model new gizmo.
An computerized beam processing line is hardly a gizmo. Even with that being the case, the Gulf Coast Welding crew wished to see if they could get the machine up and working correct from the start. That they had been excited to see what they could do.
“I don’t understand how loads money and tooling we went by the use of sooner than we decided we’d stop and await Flex to tell us discover ways to do it, nevertheless we in the end obtained there,” Maley said.
Flex Machine Devices did provide the teaching, and that’s when all of the issues started to click on on. As quickly as the basics had been coated, the Gulf Coast Welding workforce obtained further assured with the machine operations, in the end asking questions that challenged the Flex technical help workforce.
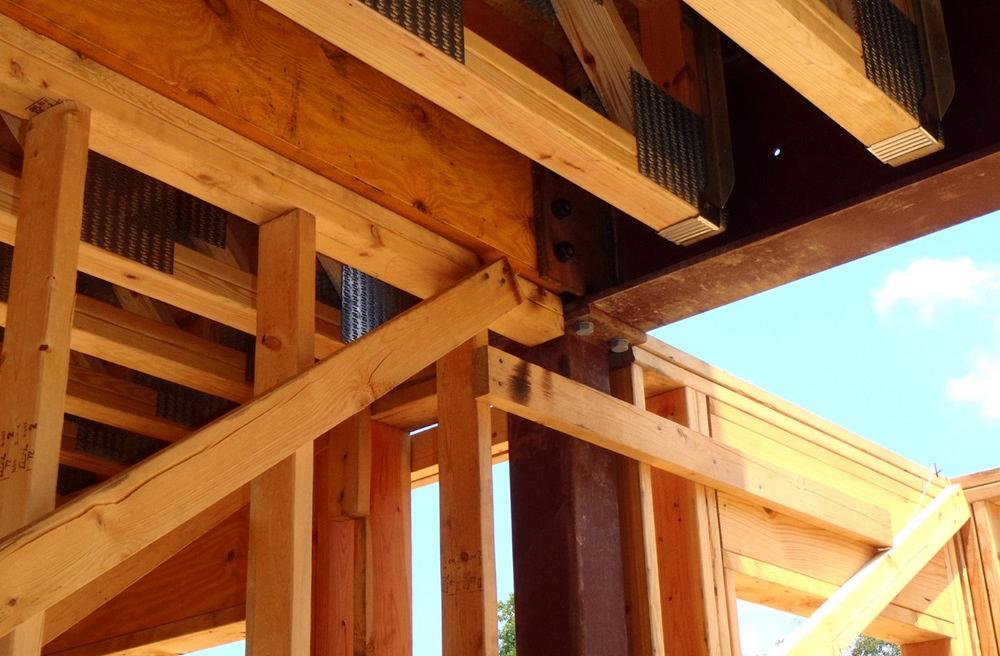
The shop moreover does structural beam work for residential functions. Alongside the Gulf Coast, properties will need to have structural helps that will stand up in direction of hurricane winds. Gulf Coast Welding
Logan Skelly, nationwide product sales supervisor, Flex Machine Devices, said he believes the FlexBeam’s user-friendly controls help to get fabricators going with their new automation.
“Our machine has a built-in graphical programming software program program that’s very straightforward to utilize. You probably can see the half, the holes or slots you are making, and the place it can possible be sitting on the mattress sooner than working this technique. This helps with the coaching curve and eliminates among the many errors that will happen when leaping into CNC-controlled instruments for the first time,” Skelly said.
Maley said that any fears the employees would possibly want had regarding the new instruments coming in to take their jobs had been shortly alleviated after they seen the machine at work. They acknowledged how the FlexBeam was going to have the flexibility to course of additional work than they ever would possibly within the occasion that that they had been to depend upon strictly handbook processes. Additional work means further earnings for the group, which is a optimistic in your complete workforce.
“We have confidence on the drilling and milling side with what we find out about this machine. We don’t have to worry about that side of points anymore,” Maley said. “Now we’re in a position to focus on the following issue.”
There are quite a few points that could be occurring inside the near future for Gulf Coast Welding. Maley said he and his companions have acquired some property, they usually’re making an attempt to find out merely how large of a facility they want to assemble. With new home, he then can consider increased supplies transfer, comparable to one of many easiest methods to feed supplies to the FlexBeam. The success alongside together with his beam processing automation moreover has him interested in together with a CNC pipe profiler and probably even channel processing instruments.
This new automated technique to metal fabricating appears to be foremost Gulf Coast Welding down a promising path for future success.