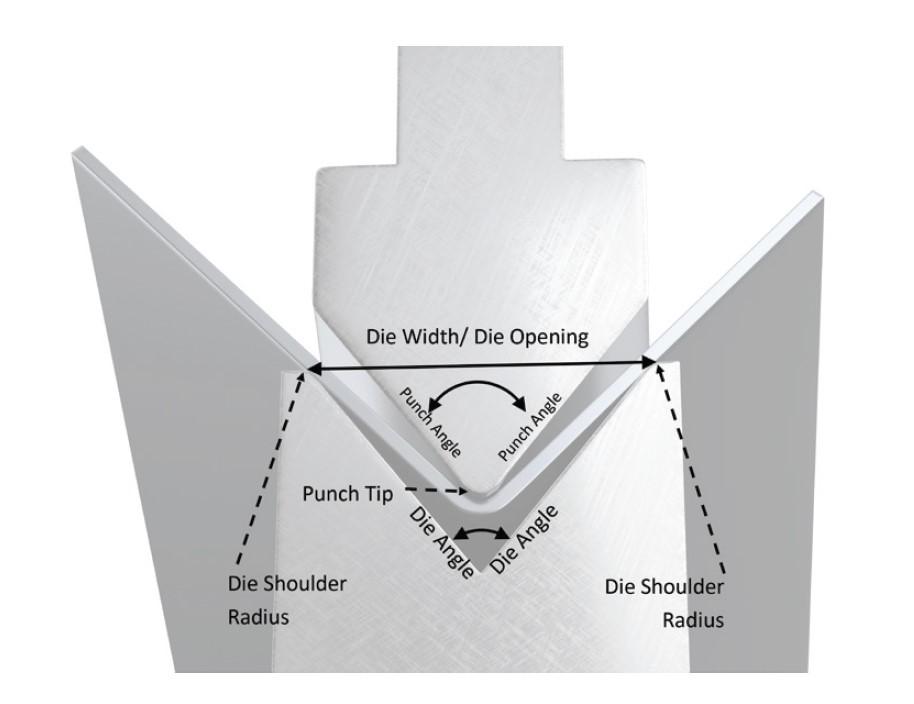
FIGURE 1. When air bending, the radius varieties as a proportion of the die opening. Nonetheless for longer bends, as a result of the punch continues to descend into the die home, the radius begins to adapt with the punch nostril radius. Why this occurs has to do with how drive is utilized on the press brake and the following strain hardening that occurs as bends get longer.
Editor’s discover: Study Half I and Half II.
Over the earlier two months, we’ve talked about how an air bend varieties as a result of the bend dimension will get longer. In shorter bends, the radius varieties as a proportion of the die opening. In longer bends, the radius wraps throughout the punch nostril. This assortment covers how and why this happens.
Why the Radius Points
I have been instructing press brakes for the ultimate 30 years and have been to an uncountable number of retailer flooring. I am always amazed at how little consideration most pay to the inside bend radius.
Do you look at the radius with gauges or pins? A giant proportion of shops don’t. So, how have you ever learnt what it is? A number of the time, prospects do not care, and neither do a retailer’s programmers. So, why should you?
Successfully, within the occasion you propose for a radius you probably can get hold of based on the bending methodology you perform and the tooling you use, then calculate the bend allowance and bend deduction based on these values, you get a sound flat clear measurement and a great half. That’s why the radius points.
Let’s assume you’ve picked among the best tooling geometry doable and achieved your predicted inside radius, not lower than over transient lengths (see Decide 1). As a result of the dimensions of the bend line will improve, the inside bend radius decreases (further on why this happens follows). A smaller radius reduces the bend allowance and the bend deduction. If we wish good parts, we must always base our numbers on the radius we actually get hold of, no matter how prolonged or transient the bend happens to be.
Some Major Phrases
How does the radius type in prolonged bends, exactly? To answer this, we have now to stipulate a few phrases. First is supplies stream, which is the metal’s potential to plastically deform and conform to the type of the tooling all through bending. Second is strain hardening (or work hardening), which is when a cloth turns into further sturdy and fewer ductile because it’s plastically deformed. Utilized tonnage refers again to the drive the press brake makes use of to bend the material. Then we have the ii>inside bend radius, which is the radius on the inside flooring of the bend. The inside bend radius is influenced by every the tooling geometry and bending drive.
Transfer and Stress
Inside the preliminary stage of forming, at lower tonnage ranges, the material begins to bend and stream comparatively freely between the die shoulders. At this degree, the material has not however undergone very important strain hardening and retains plenty of its ductility. The radius formation at this stage adheres to the 20% rule, which states that air-bent supplies varieties its radius as a proportion of the die opening. The rule’s title comes from 304 stainless steel, which varieties a radius that’s between 20% and 22% of the die opening. For light steel, our baseline supplies, the radius varieties at about 16% of the die opening.
As a result of the utilized tonnage will improve, the punch penetrates deeper into the die. Concurrently, the material experiences further very important plastic deformation, inflicting strain hardening, elevated yield vitality, and decreased ductility. The material turns into further proof against extra deformation. This elevated resistance begins to limit the material’s potential to stream.
Inside the first of this assortment, I stated that “tonnage will improve exponentially with dimension.” “Exponentially” is not exactly the proper descriptor. In case your supplies is fixed, its bending second stays the an identical; it doesn’t change. So, what’s really occurring proper right here? The issue has to do with the press brake itself.
An prolonged bend requires further drive, and the additional drive you apply to bend, the additional the facet frames, mattress, and ram flex, reducing the utilized drive on the bend. That’s on account of a number of of the drive goes into the brake. To compensate for that flexing, we apply further drive as the material penetrates deeper into the die home. We’re nonetheless rising drive to carry out the bend. What happens as soon as we improve drive? We improve the amount of stress or work hardening of the material on the extent of bend.
Stress hardening reduces supplies stream, and it seems counterintuitive that the material would wrap further tightly throughout the punch nostril radius, lowering the inside bend radius. No matter strain hardening reducing ductility, the elevated drive (tonnage) overcomes that resistance, forcing the material to adapt further intently to the punch nostril radius.
The Mechanics of Stress Hardening
The higher tonnage presents additional vitality to deform the strain-hardened supplies. Although the material resists deformation due to strain hardening, the elevated drive is ample to proceed deforming it. The punch penetrates farther into the die, mechanically forcing the material to wrap throughout the punch nostril. This bodily movement reduces the inside bend radius to the aim the place it conforms to the punch nostril radius.
Observe that the material adjoining to the punch nostril undergoes very important plastic deformation. So, even supposing the common ductility is decreased, the material is compelled to adapt to the punch nostril because of the concentrated drive.
As the material strain-hardens, its yield vitality will improve, requiring further drive for any additional deformation. The elevated tonnage ought to sufficiently exceed the strain-hardened supplies’s new, elevated yield vitality. That’s how, no matter strain hardening and decreased supplies stream, the inside radius nonetheless reduces, inflicting the material to wrap further tightly throughout the punch.
At low tonnage, the inside bend radius is determined by the die opening, the 20% rule, the place the material flows merely. The inside radius is identical as a proportion of the die opening, and folks percentages fluctuate by supplies kind.
As a result of the drive will improve, however, the material begins to strain-harden, and ductility decreases, nevertheless the elevated tonnage continues to deform the material. At the moment, the inside radius decreases as the material conforms further to the punch profile.
It’s not about elevated stream, nevertheless elevated drive. That is, we get a tighter bend radius not on account of the material flows further nevertheless on account of the higher drive overcomes the material’s resistance, mechanically shaping it.
The Outcomes of Concentrated Stress
The realm of the bend that contacts the punch, what we identify the land area, experiences extreme localized stress. This stress can usually exceed the elevated yield vitality due to strain hardening, allowing extra deformation.
Even the material’s last tensile vitality (UTS) comes into play. UTS is elevated than the yield vitality, even after strain hardening. You usually need loads drive to complete a bend, you probably can surpass the UTS domestically, inflicting plastic deformation and fracture.
In reality, there are the material limits. Excessive deformation of strain-hardened supplies may end up in cracking or failure, notably with sharp or minimum-radius bends. Each supplies could also be deformed solely loads sooner than failure. That is referred to as the ductility threshold.
A smaller punch nostril radius will improve the prospect of cloth failure. Adjusting die angles and radii can have an effect on how the material deforms, so watching the die geometry is essential. Solely apply enough drive to achieve the required bend with out overloading the material. Slower bending speeds may even reduce the prospect of sudden supplies failure.
So, Are We Really Air Forming?
By considering the material’s strain-hardening conduct and the outcomes of utilized drive, we’re capable of greater predict and administration the bending course of to achieve the required outcomes.
To analysis, take into consideration the following course of when forming longer bends: (1) The material bends merely, flowing into the die with minimal resistance; (2) the material’s resistance grows due to strain hardening as drive will improve; (3) as a result of the punch pushes deeper, no matter resistance, the material is pressured to wrap throughout the punch nostril, and the punch’s mechanical movement overcomes the material’s elevated resistance.
Everyone knows how radius formation modifications as our bends get longer. Considering this, are we nonetheless air forming as a result of the bend will improve pressure and penetration depth? We’ll dive deep into this question subsequent month. We’ll moreover ponder how the completely completely different forming methods affect all this. Lastly, we’ll cowl apply what we’ve realized—with the intention of producing greater parts, from engineering onward.