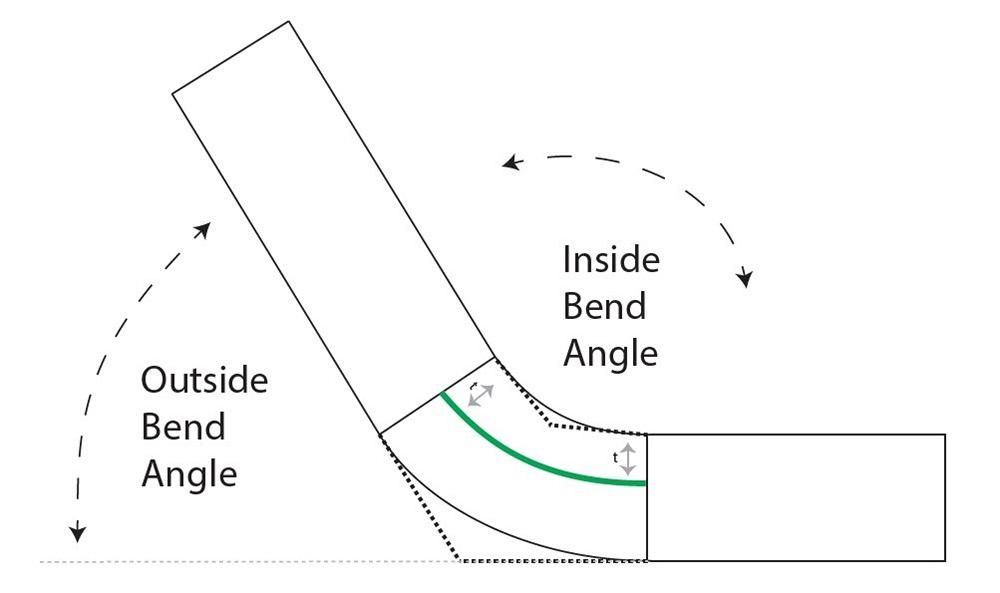
FIGURE 1. Exterior bend angles are measured from the floor of the bend.
Albert Einstein as quickly as acknowledged, “The additional I be taught, the additional I perceive how loads I don’t know.” That is named the paradox of information. It reminds us of the vastness of the unknown and the countless nature of the pursuit of information.
For the earlier various months, we now have been discussing the inside radius of the bend, along with its significance in design and manufacturing. So, what’s subsequent? How a few check out the springback subject? What’s it, and what does it ought to do with the inside bend radius? Properly, as you may want already guessed, you’re about to hunt out out.
What Is Springback?
You possibly know what springback is, nonetheless in case you’re new to bending or need a refresher, listed under are the basics: Whilst you sort sheet metal (or the remainder that may bend, for that matter), you’ll be aware varied portions of springback. The character of springback varies with the bending method, nonetheless for this dialogue, we’ll give consideration to air bending. Moreover know that I’ll be referring to open air angles, as measured from the floor of the bend (see Decide 1).
Whilst you launch supplies from the load (energy), the bend relaxes as the material tries to return to its distinctive flat place. It doesn’t make all of it the best way wherein once more to flat, nonetheless the angle does spring once more open a certain amount. The press brake air-bends to the bending angle, which is the required angle plus the required ranges of overbend for springback. When sheet metal is launched from the load, it releases the ability put into the bend and the angle relaxes to the bent angle, the angle that the material achieves as quickly because the springback has been launched (see Decide 2).
Springback is part of the final word developed bend radius. When the bending angle relaxes, so does the inside radius of the bend. It relaxes a small amount, similar to the bend angle. Can you calculate it? Positive. Can or not it is used? Sure. And proper right here’s how.
Calculate the Springback Problem
Divide the bending angle by the bent angle and we get a multiplier value known as the springback subject (Sf), which we use to calculate the exact inside radius of the bend. As an illustration, in case you might be working with a cloth that has 2 ranges of springback, and it’s advisable to make a bend with a remaining angle of 90 ranges, it’s advisable to overbend to an outside angle of 92 ranges: Sf = 92 ranges/90 ranges = 1.0222
What do you do with that amount? You use it as a multiplier, which is then utilized to the distinctive anticipated inside bend radius. If the inside bend radius is 0.062 in., you multiply the beginning inside radius value by Sf to hunt out the exact inside bend radius after the bend relaxes: 0.062 × 1.0222 = 0.063. This supplies you your relaxed inside bend radius, which you then use to calculate the bend allowances (BAs), bend deductions (BDs), and outside setbacks.
Springback isn’t restricted to 2 ranges, in any case. Counting on the material kind, the springback is likely to be a lot much less and even rather more. We’ve to calculate Sf using the exact angles involved, which ceaselessly requires bending various verify gadgets sooner than making any calculations.
Two Ranges Is Not Two Ranges
You is more likely to be asking, is that this a sort of situations the place two plus two equals 5? No, it is not. That type of math solely works in politics. I’m referring to the reality that merely understanding a bend springs once more by 2 ranges doesn’t give us our springback subject. The Sf modifications counting on what the bending and bent angles are:
- 47-degree bending angle/45-degree bent angle = 1.0444 Sf
- 92-degree bending angle/90-degree bent angle = 1.0222 Sf
- 137-degree bending angle/135-degree bent angle = 1.0148 Sf
As soon as extra, although each of these angle pairs is 2 ranges apart, the value for Sf varies with the angle of bend, which moreover impacts the BA, BD, and setback calculations. As everybody is aware of, flawed calculations equal harmful elements.
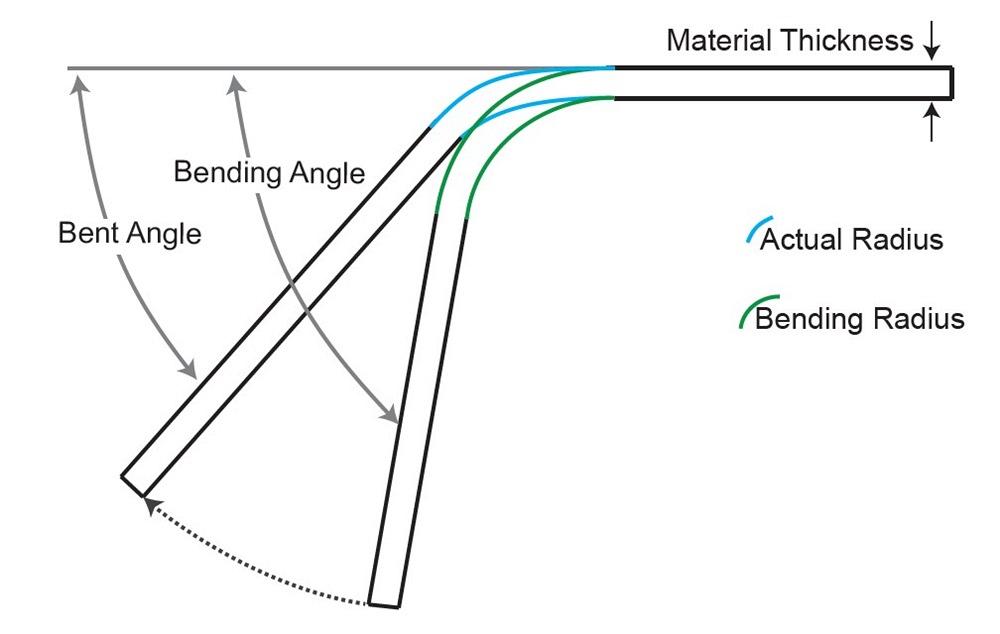
FIGURE 2. The press brake overbends to the bending angle, then releases stress and permits the bend to loosen up and spring once more to the bent angle. The bend radius relaxes too—not by loads, nonetheless adequate to affect your bend allowances and bend deductions.
Take into consideration a job by which we receive a 0.063-in. radius in 0.063-in.-thick supplies on the bending angle, sooner than springback. When the angle springs once more 2 ranges, the radius opens barely. Assuming a k-factor of 0.446, how does this affect our bending calculations? Check out the beneath examples:
EXAMPLE 1
Bending angle = 92 ranges
Radius at bending angle = 0.063 in.
BA at bending angle = 0.14628 in.
BD at bending angle = 0.11468 in.
Bent angle = 90 ranges
Sf = 92/90 = 1.0222
Radius at bent angle = 1.0222 × 0.063 in. = 0.0644 in.
BA at bent angle = 0.1453 in.
BD at bent angle = 0.1095 in.
EXAMPLE 2
Bending angle = 47 ranges
Radius at bending angle = 0.063 in.
BA at bending angle = 0.07473 in.
BD at bending angle = 0.034845 in.
Bent angle = 45 ranges
Sf = 47/45 = 1.04444
Radius at bent angle = 0.063 in. × 1.04444 = 0.0658 in.
BA at bent angle = 0.07375 in.
BD at bent angle = 0.032954 in.
We’re talking modifications of solely a thousandth or two. The modifications are minimal, nonetheless they’re nonetheless there.
Do We Truly Should Worry?
That relies upon upon your half tolerances and easily how right your elements should be. It moreover will depend upon what variety of bends you have received in a single workpiece.
If you’ve received a tolerance of ±0.020 in. and various bends, then the springback subject might be worth considering, as every further bend compounds the amount of error you’ll be aware in that half. In case your tolerances are merely ±0.010 in., then it is a pretty good idea to incorporate the springback take into consideration your calculations.
Measuring the Radius
A novel diploma of springback modifications your inside bend radius. For precision work involving various bends, even the smallest change can throw each half off. So, in the event you want to be right, how do take a look at for such minute modifications?
Pin gauges work good nonetheless are pricey, and people are inclined to lose them. I prefer to advocate making your private radius gauge set. Create a single DXF file for a single gauge, then, on the laser or waterjet, scale it up or down for the radius it’s advisable to measure.
You’ll create a single gauge and let it journey with the work folder. Alternatively, you probably can create two full items, one for the forming division and one different in prime quality administration. Make a set for everyone working throughout the press brake house.
Small Numbers, Huge Have an effect on
For the previous couple of months, I have been hammering the importance of the inside bend radius to any problem that requires bending. It is the coronary coronary heart of one thing you are trying to carry out. In case you get that incorrect, guess what? You get accomplished elements which might be additionally incorrect.
Tight tolerances in precision bending are like micro organism. They is likely to be very small, nonetheless they’ve a big impact.
Small numbers matter. A thousandths error on one bend will not sound like an enormous deal, nonetheless what a few half that has a dozen bends or further? Sooner than it, a tiny error can snowball into a big draw back.
Like multiplying micro organism, the tolerances stack up, and sooner than it, you’ve scrapped a classy, and likely very pricey, half.